Material procurement is the process of sourcing, acquiring, and managing materials and goods required for production and operational requirements. It involves the identification of needs, selection of suppliers, negotiation of contracts, and the logistics of delivery, ensuring that the materials meet necessary quality and cost criteria while maintaining adherence to timelines and regulatory standards.
Key Benefits
– Cost Efficiency: Material procurement ensures the strategic sourcing of materials at the best prices, reducing overall procurement costs and enhancing budget management without sacrificing quality or performance.
– Supplier Relationship Management: It helps in building strong relationships with suppliers by ensuring timely payments and consistent orders, leading to better negotiation terms and preferred customer status.
– Inventory Optimization: By accurately assessing material needs and timing purchases, material procurement prevents overstocking or stockouts, leading to more efficient inventory management and reduced holding costs.
– Risk Mitigation: Material procurement involves assessing and analyzing supplier capabilities, quality, and reliability, effectively reducing supply chain risks and ensuring continuity in material availability.
– Process Efficiency: Automating and streamlining material procurement processes lead to reduced manual errors, faster cycle times, and enhanced compliance with organizational policies.
Related Terms
– Cost Efficiency: Material procurement ensures the strategic sourcing of materials at the best prices, reducing overall procurement costs and enhancing budget management without sacrificing quality or performance.
– Supplier Relationship Management: It helps in building strong relationships with suppliers by ensuring timely payments and consistent orders, leading to better negotiation terms and preferred customer status.
– Inventory Optimization: By accurately assessing material needs and timing purchases, material procurement prevents overstocking or stockouts, leading to more efficient inventory management and reduced holding costs.
– Risk Mitigation: Material procurement involves assessing and analyzing supplier capabilities, quality, and reliability, effectively reducing supply chain risks and ensuring continuity in material availability.
– Process Efficiency: Automating and streamlining material procurement processes lead to reduced manual errors, faster cycle times, and enhanced compliance with organizational policies.
References
For further insights into these processes, explore Zycus’ dedicated resources related to Material Procurement:
- Making Procurement Performance Count – Part 1: Evolution of Procurement
- Boosting Financial Efficiency: The Role of an Accounts Payable KPI Dashboard
- Procurement: From the eyes of a CPO
- Cost Optimization Secrets: Strategic Sourcing and Vendor Management Realign Costs and Protect Revenues
- Broadridge’s Procurement Evolution: Strategy, AI & Transformation
White Papers
Master the UK Procurement Act 2023: Ensure Compliance & Drive Procurement Excellence
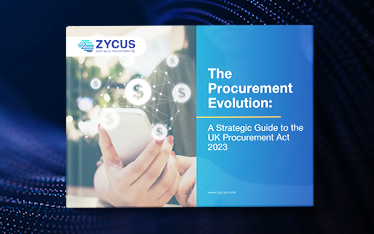
Filter by
Consolidated Invoice
A Consolidated Invoice is a single invoice document that aggregates multiple individual transactions or services provided over a certain period,
Compliance Scorecard
A Compliance Scorecard is a structured tool used within procurement processes to evaluate and ensure that all sourcing activities adhere
Contract Addendum
A contract addendum is a formal document that modifies or adds terms to an existing contract without altering its original
Contract Authoring
Contract Authoring refers to the process of creating, drafting, and preparing contracts for agreement and execution. It involves outlining terms,
Contract Review
Contract Review is the structured analysis and evaluation of contract terms to ensure compliance, mitigate risks, and align with organizational
Bid Response
A Bid Response is a formal reply by a supplier or vendor to a Request for Proposal (RFP) issued by