Collaborative Planning, Forecasting, and Replenishment (CPFR) is a supply chain management practice where multiple trading partners collaboratively coordinate planning, forecasting, and replenishment activities to improve supply chain efficiency and customer service by synchronizing production and replenishment processes based on shared information and joint forecasting efforts.
Key Benefits
– Enhanced Collaboration: CPFR facilitates improved collaboration between supply chain partners, leading to better alignment of goals and strategies. This collaborative effort ensures that all parties are working towards common objectives and sharing vital information.
– Improved Forecast Accuracy: By jointly developing and sharing forecasts with supply chain partners, companies can achieve higher accuracy. This leads to more reliable demand forecasts, reduced forecast error, and ultimately, a more efficient supply chain.
– Inventory Reduction: Through shared planning and visibility across the supply chain, CPFR helps in maintaining optimal inventory levels, reducing excess stock and mitigating shortages. This ensures that inventory is aligned with actual demand.
– Increased Sales and Customer Satisfaction: With better inventory management and demand fulfillment, companies are more likely to meet customer needs promptly, leading to increased sales and improved customer satisfaction levels.
– Cost Reduction: CPFR reduces costs associated with excess inventory, expedited shipping, and stockouts by enhancing efficiency and reducing misalignments within the supply chain. This leads to overall reductions in operating expenses.
Related Terms
– Enhanced Collaboration: CPFR facilitates improved collaboration between supply chain partners, leading to better alignment of goals and strategies. This collaborative effort ensures that all parties are working towards common objectives and sharing vital information.
– Improved Forecast Accuracy: By jointly developing and sharing forecasts with supply chain partners, companies can achieve higher accuracy. This leads to more reliable demand forecasts, reduced forecast error, and ultimately, a more efficient supply chain.
– Inventory Reduction: Through shared planning and visibility across the supply chain, CPFR helps in maintaining optimal inventory levels, reducing excess stock and mitigating shortages. This ensures that inventory is aligned with actual demand.
– Increased Sales and Customer Satisfaction: With better inventory management and demand fulfillment, companies are more likely to meet customer needs promptly, leading to increased sales and improved customer satisfaction levels.
– Cost Reduction: CPFR reduces costs associated with excess inventory, expedited shipping, and stockouts by enhancing efficiency and reducing misalignments within the supply chain. This leads to overall reductions in operating expenses.
References
For further insights into these processes, explore the following Zycus resources related to Collaborative Planning, Forecasting, and Replenishment (CPFR):
White Papers
Master the UK Procurement Act 2023: Ensure Compliance & Drive Procurement Excellence
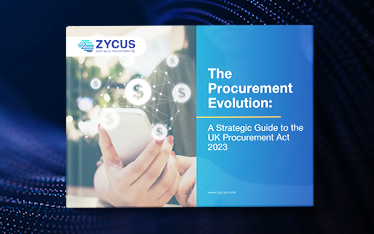
Filter by
Consolidated Invoice
A Consolidated Invoice is a single invoice document that aggregates multiple individual transactions or services provided over a certain period,
Compliance Scorecard
A Compliance Scorecard is a structured tool used within procurement processes to evaluate and ensure that all sourcing activities adhere
Contract Addendum
A contract addendum is a formal document that modifies or adds terms to an existing contract without altering its original
Contract Authoring
Contract Authoring refers to the process of creating, drafting, and preparing contracts for agreement and execution. It involves outlining terms,
Contract Review
Contract Review is the structured analysis and evaluation of contract terms to ensure compliance, mitigate risks, and align with organizational
Bid Response
A Bid Response is a formal reply by a supplier or vendor to a Request for Proposal (RFP) issued by